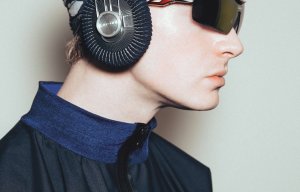
Stoll to display its latest collection at Milan Design Week
The two entrepreneurs looked for an option that would not require wasting resources, endless transport routes and excessive use of chemicals.
18th July 2017
Innovation in Textiles
|
Bönnigheim
With their idea of breathing new life into worn-out truck tarpaulins and making them into weatherproof, one-of-a-kind bags for individualists in the big city jungle, the graphic designers, Daniel and Markus Freitag, truly reflected the spirit of the times in 1993 and have written an impressive success story since then.
“In 1993, there were no appropriate bags for us to transport our designs on a bicycle, keeping them safe and dry. So, we spontaneously made some ourselves. Robust, long-lasting and sustainable. Can used items be utilised purposefully in a different context? What does a product need to look like, so that it doesn’t leave anything harmful at the end of its lifecycle? We have always been dealing with such questions,” say Daniel and Markus Freitag.
“And when we were searching for new workwear for our employees and understood how the global textile industry handles resources, the environment and its workers in some cases, it quickly became clear that we would prefer to take the matter of clothing into our own hands.”
According to the two entrepreneurs, they looked for an option that would not require wasting resources, endless transport routes and excessive use of chemicals. The textiles had to be manufactured at fair conditions nearby and be suitable for wearing in the factory, as well as after work. Once they have been worn out, it should be possible to throw them on the compost, where they can biodegrade without any residues, with a clear conscience.
“In order to meet these requirements, we went back to the beginning of the natural development chain: to the fibre. To be able to guarantee the biodegradability of our textiles, once they have been worn out, we searched for natural and renewable resources, which are available in our latitudes. So, the choice fell on the cultivated plants, linen and hemp, which thrive magnificently along the Atlantic coast, do not require much water and fertilisers and textile fibres have already been gained from their raffia for a long time,” they explain.
“For lighter fabrics, Modal is also used – this is obtained from local beech trees in Austria. In Lombardy, we found a weaving mill, which is able to produce our trouser fabric according to our own ideas, and our garments are ready-made in Poland. Overall, it took five years from the original idea until we were able to deliver the first completed garments – including a strict test of the shirts and trousers in our own factory and numerous self-wearing tests.”
During the development of F-ABRIC, the company conducted its own composting tests on its factory roof garden. When it then came to the product launch, the brand searched for an institution, which could competently and independently provide evidence that its textiles are 100% biodegradable after unscrewing the metal buttons and the soil is not polluted with harmful substances after their decomposition. The experts of the Hohenstein Group offered a customised tool for these requirements, with its standardised soil-burying tests to determine the biodegradation.
“The tests in Hohenstein concluded that our textiles are almost completely decomposed after six months. They passed the eco-toxicological tests that were conducted. As our products are made of natural fibres, the Hohenstein experts recommended a soil-burying test to us under open land conditions. Burying in a laboratory would also have been conceivable, but it was important to us for the natural climate change over half a year to flow into the investigations,” say Daniel and Markus Freitag.
“We did not think that the decomposition process would be so quick. So far, there has not been any recognised international standard for the degradability of textiles, therefore, the biodegradation tests in Hohenstein can be an important instrument for textile companies, when it comes to scrutinising the last step of the product cycle.”
Business intelligence for the fibre, textiles and apparel industries: technologies, innovations, markets, investments, trade policy, sourcing, strategy...
Find out more