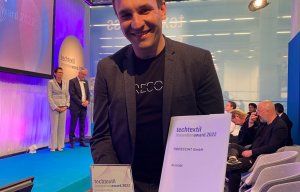
Award for the smallest reinforced composite...
RWTH Aachen spin-off to launch new metal-coated basalt and thermoplastic-coated glass fibres for composite and shielding applications.
24th November 2021
Innovation in Textiles
|
Aachen, Germany
FibreCoat GmbH, a composite materials spin-off from the Institute of Textile Technology (ITA) at RWTH Aachen University in Germany, has closed a $3 million Series A round of financing with Goose Capital, Phoenix Venture Partners, b.value AG, Nova by Saint-Gobain and the TiE Houston Angels.
“These strong investors offer a knowledgeable background in materials and a diverse network into the markets we serve as we lay the foundation for scaling our technology to increase our capacity from ten tons per month to 60 tons per month in 2022,” said FibreCoat CEO Robert Brüll.
The company has developed new coated fibres for composite and shielding applications and its first products are AluCoat, metal-coated basalt fibres used for electromagnetic shielding and conducting applications, and PolyCoat, thermoplastic-coated glass fibres used for strengthening and light weighting applications.
The capital raised is being used to expand the FibreCoat team to increase sales and marketing activities as the company looks to increase capacity and build new partnerships in the construction, electronics and automotive industries.
Quality advantages
The coated fibres provide substantial quality advantages due to the single-filament coating and the tunability of the materials in terms of coating thickness, homogeneity and cores. FibreCoat produces application and customer-specific bicomponent filaments for a wide range of applications resulting in disruptive advances in the composite and EMI shielding industries. It provides a significant advantage over other technologies due to its high speed and one-step process, with substantial-quality advantages resulting from the single-fibre coating. The high-performance fibres not only improve existing products but enable completely new mass market applications in areas ranging from light-weight EMI shielding in electric vehicles and defence applications to drapeable EMI shielding fabrics for smart textiles or wallpapers in hospitals.
“In addition to high coating flexibility, our extensive network for the customer-specific processing of coated fibres differentiates us from our competitors,” said Brüll. “Our first market-ready product, AluCoat, saves up to 90% in CO2 emissions during production when compared to alternative materials such as solid metal fibres and aluminium foils and sheets, while also being fully recyclable.”
Business intelligence for the fibre, textiles and apparel industries: technologies, innovations, markets, investments, trade policy, sourcing, strategy...
Find out more