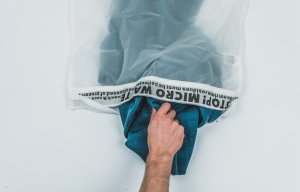
New self-cleaning washing bag from Isbjörn of Sweden
The cleaning effect is based on a combination of both hydrolysis and gas flow dynamics.
9th October 2019
Innovation in Textiles
|
Remscheid
Current techniques of polymer filters cleaning involve the use of chemical solvents, which come with a lot of disadvantages. TEG and similar chemicals are not only costly, toxic and highly flammable, but also harmful to the environment; therefore they have to be disposed of extensively.
The machine construction company BB Engineering – subsidiary of Oerlikon Barmag and Brückner Maschinenbau – in Remscheid, Germany, has developed an alternative filter cleaning solution for polymer filters without toxic solvents. It is marketed under the trade name WFC – White Filter Cleaning. WFC is designed to clean filter elements – candles or discs – from production lines processing polymers like PETP, PA6.
The cleaning effect is based on a combination of both hydrolysis and gas flow dynamics. Super-heated steam flows through the polluted filter elements in reverse direction (compared to regular polymer flow). After draining out the melt with the support of gravity and nitrogen pressure as much as possible, the remaining melt inside the filter insert is pushed out by super-heated steam. The steam is injected via ports into the cleaning vessel until a pre-set pressure (up to 8 bar) is reached.
During this fill-up time the steam reduces the viscosity of the melt inside the filter insert by means of a hydrolysis degradation. After that, the pressure is released by means of a sudden opening of a decompression valve (gas flow dynamics effect). This cycle of hydrolysis and decompression is repeated multiple times, each cycle removing some polymer from the filter into a waste collector. The decompression process is derived from the deecom process owned by B&M Longworth, UK, with which BB Engineering is collaborating.
“This cleaning method is as effective as to substitute any other main cleaning methods, such as cleaning using solvents. After having removed the polymer using WFC, the filter elements can be transferred to regular subsequent final cleaning steps,” the company reports.
The main advantages of WFC include:
BB Engineering WFC involves the following main components: preheating and draining station for the filter insert; nitrogen supply, including control box; steam supply with safety devices and control system; high-speed decompression valve, and waste collecting/condenser tank for transferring the superheated steam into liquid water.
The cleaning equipment is also suitable for filters of other manufacturers and for cleaning other machine parts such as spinnerets, breaker plates, valves and melt pipes (special adapters may be required).
BB Engineering says it demonstrated the effectiveness of WFC in the case of filters from BO-PET lines and at large candle-type-filters from a PA6 chips production system. Typical methods for evaluating the cleaning effect are to compare the bubble point values and the weight per filter element in new condition versus values after cleaning.
From the end of 2019 onwards, BBE will have a WFC demonstration system on hand in Remscheid. This system will clean the filters of BBE´s PETP recycling line. The internal size of the cleaning chamber is 890 mm Ø x 880 mm height.
Business intelligence for the fibre, textiles and apparel industries: technologies, innovations, markets, investments, trade policy, sourcing, strategy...
Find out more