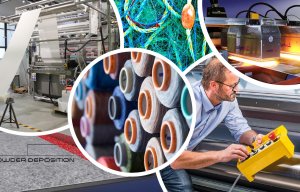
Transition could save wet processors $25 billion
Upgrade exploits pressure drop between successive cylinders in the machine.
11th June 2024
Innovation in Textiles
|
Obertshausen, Germany
Karl Mayer Group is introducing the patented Cascade system enabling considerable energy savings to be made on the cylinder dryers of its Prosize sizing machines and Bluedye dyeing plant for warp preparation.
Energy consumption has become a major issue for textile manufacturers, accounting for between 5-15% of overall costs and a ton of steam cost between $20-27 per ton in 2021, according to a study by the Swiss-headquartered ITMF (International Textile Manufacturers Federation). The price of energy has risen considerably in subsequent years, so it makes sound sense to reuse steam wherever possible.
“Cascade recirculates parts of the process steam in dryers by exploiting pressure drop between the successive cylinders, enabling efficient energy recycling within the machine,” explains Karl-Heinz Vaassen, head of textile drying at Karl Mayer.
With steam heating, the highest working pressure prevails in the first cylinder section and emits large amounts of energy which condenses without temperature loss.
The resulting hot condensate is not immediately discharged from the machine, but is instead fed into a flash tank, where vapor exhaust is formed as a result of the pressure reduction. In conventional systems, the carrier medium for gases is only created in the return line towards the boiler house and is eliminated as undesirable. Instead of being utilised in the process, it escapes into the environment. With the Cascade system, this freshly recycled steam is used for the heat supply in the second cylinder section.
The recycled steam is intelligently mixed with live steam and raised to the level of the required process conditions for use in the cylinder section at the end of the dryer. Here, the fabric moisture is reduced to the desired residual value at medium pressure and temperature conditions.
With a view to the Asian market, a dryer with 14 cylinders and an annual running time of 7,000 working hours can achieve cost savings of up to $17,000 per year.
A dashboard sensor provides real-time data on the amount of steam circulating in the circuit, from which the corresponding reduction in CO2 equivalents can be calculated.
Cascade will be standard on new Prosize systems and the first sizing machine with the upgrade will be delivered to a manufacturer in Europe shortly. It will then be integrated into other dryer types and made available for the Bluedye.
Business intelligence for the fibre, textiles and apparel industries: technologies, innovations, markets, investments, trade policy, sourcing, strategy...
Find out more